Medicine
Fine-tuning customized medical technology
From hip prostheses to artificial heart circuits: pioneering medical technology has been developed in Bern since 1963. A decisive role in this context was played by a research workshop that became a part of the University of Bern in 1989.
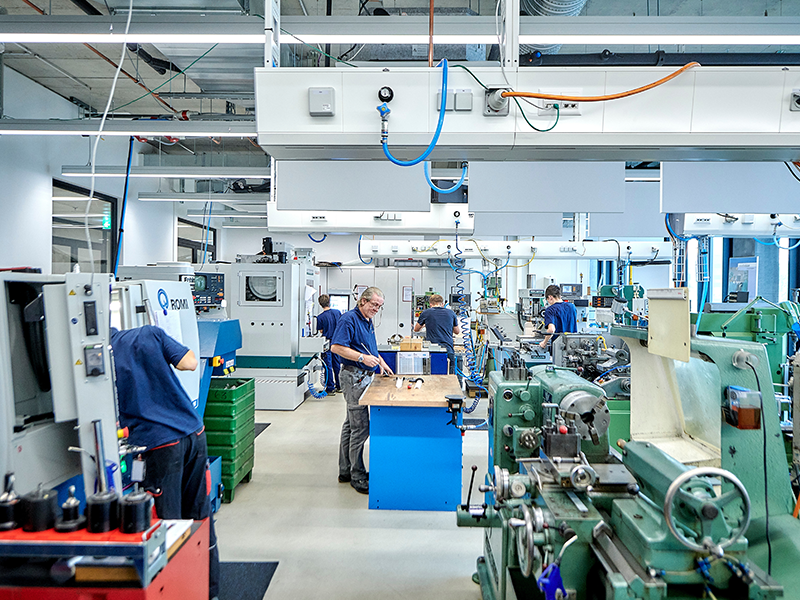
Metal shavings pile up in a container. It smells of machine oil. Between screwdrivers and lathes, five men in cargo pants and steel cap shoes stand and saw, grind, measure parts or program computer-controlled milling and turning machines. In the midst the workshop manager: "We make top-quality mechanical components for medicine here," he says.
The succession of a pioneer
Since 1991, the federally certified master mechanic has overseen the workshop, which has changed location and institutional affiliation several times since then. Today, it belongs to the ARTORG Center for Biomedical Engineering Research and is located in the Swiss Institute for Translational and Entrepreneurial Medicine sitem-insel.
Much more important to Rohrer than the location is that he was still able to meet the workshop's founder, Maurice E. Müller, himself. "That was inspiring and laid the foundation for all the expertise in biomechanics and manufacturing we've developed here over time.
"Meeting Maurice E. Müller was inspiring and laid the foundation for all the expertise in biomechanics and manufacturing we've developed here over time."
– Urs Rohrer
As a full professor at the University of Bern, the visionary surgeon and orthopedist had spurred medical technology research in Bern between the 1960s and 1980s. In his opinion, innovation progressed best when all competencies - from medicine to conception and technical implementation - were in-house.
Research and craftsmanship under one roof
Nikola Saulacic, Leader Clinical Research at the Department of Cranio-Maxillofacial Surgery at Inselspital, Bern University Hospital has been a client of the ARTORG workshop for 10 years. “In the workshop, I have always received a friendly welcome and very competent advice. The new location in sitem-insel is certainly an advantage. For production, there is space for state-of-the-art machinery here and the workshop is closer to us, which makes cooperation much easier."
Saulacic researches the regeneration of the jawbone after tooth removal, fractures or tumor surgery. The periosteum plays a decisive role in the bone healing and repair. For this purpose, he needed to know how much mechanical stress an inserted titanium plate puts on it. Through the recommendation of colleagues, he came to the ARTORG workshop.
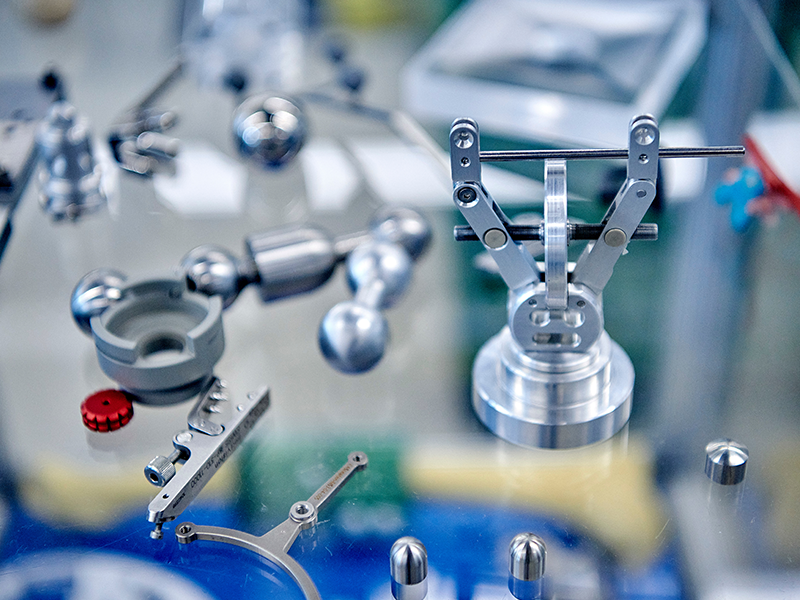
His impression of the collaboration is very positive to this day: "Two models have developed from the basic idea, for extra-oral and intra-oral use. Two years ago, the project was supported by the Swiss National Science Foundation. We are currently analyzing the collected data and now hope that we can bring the intra-oral model to clinical application".
"A solution specific to my problem"
Samir Abou-Ayash, senior physician at the Clinic for Reconstructive Dentistry and Gerodontology at the ZMK University of Bern, likewise perceives collaboration with the workshop as an asset: "The first thing Urs did was to come to me at the clinic to get an exact picture of the experimental setup. I found that very trust-inspiring". Similar to Dr. Saulacic, he too initially had a vague idea of how he could design the fixtures for testing the wear of dental prostheses. But he was unsure to what extent his idea was feasible or even fulfilled the research purpose:
"Although I could have simply ordered various components for my project externally, I still had no clear idea of what I actually needed," says Dr. Abou-Ayash. "This personal attention and collaboration to find a solution specific to my problem was much better than if I had had to come up with it all myself. Here Urs has helped me enormously with his experience."
"This personal attention and collaboration, (...) were much better than if I had had to come up with it all myself."
– Samir Abou-Ayash
In addition to the research institutions of the university and the Inselspital Departments, the workshop's clientele also includes ARTORG's own research groups and some startup companies. Furthermore, platforms at sitem-insel can also use the workshop for research and development of medical technology via the sitem-insel Support Funds.
25 years training apprentices
Next to the highly customer-oriented services, MDP has another core task: For 25 years, polymechanic apprentices have been trained here.
"What is special about us is that apprentices grasp the entirety of a project, i.e. they know the "intended use" and do not just produce parts in isolation."
– Urs Rohrer
Candidates for a 4-year apprenticeship as a polymechanic EFZ have the opportunity to complete it at the ARTORG Center. Starting off their apprenticeship, boys and girls receive six months of basic training at the Center for Space and Habitability. Afterwards, they can commence further training and specialization either at the ARTORG Center or at the Department of Chemistry, Biomedicine and Pharmacy - either in the direction of medical applications or in space research, where parts of the ROSETTA mission also originated
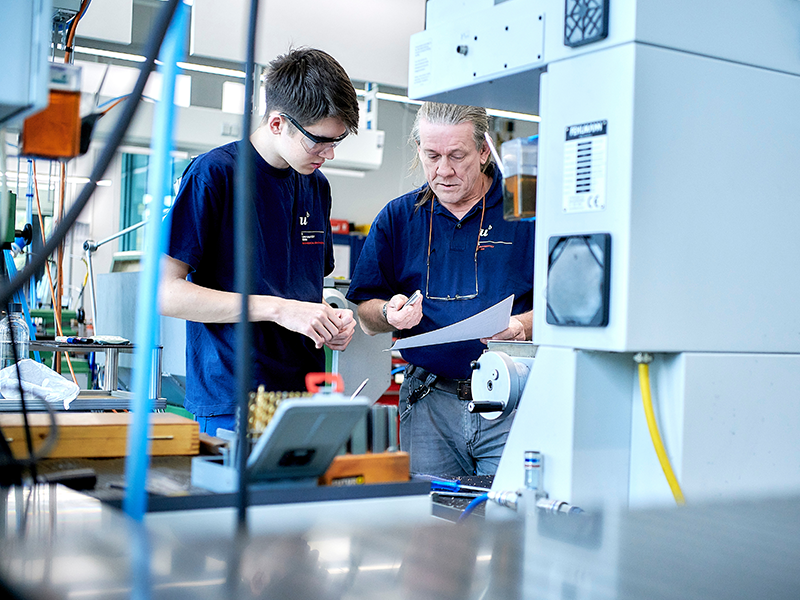
"The three workshops at the University of Bern work closely together to train apprentices," explains Urs Rohrer. "What is special about us is that apprentices grasp the entirety of a project, i.e. they know the "intended use" and do not just produce parts in isolation. This requires creativity, because there is not just one solution for a problem".
Heart circuits out of the workshop
This was also the experience of Janosch Schär, who had to manufacture a device for fixing a heart valve for his final apprenticeship exam this spring at ARTORG. "This was challenging because my design is supposed to hold both biological and artificial heart valves in such a way that the fluid mechanics in the experiment correspond exactly to the behavior in a patient's heart," Janosch explains.
For ten years, the ARTORG Center has been developing so-called "flow loops" that simulate a cardiac cycle by means of a pump and water chambers. This helps physicians gain a deeper insight into heart valve function and answer specific research questions. The Bern Flow Loops exemplify how such collaboration between female physicians, fluid mechanics specialists and polymechanics can advance cardiac research. Due to their high quality, other research institutions are now also contracting these flow loops from ARTORG for their projects.
At the pulse of Bern's MedTech development
The apprenticeship in the midst of medical technology innovation features projects that have particularly high demands on precision and material quality due to their medical application. Accordingly, individual parts are mainly made of special materials such as stainless steel, titanium or high-strength aluminum, which are difficult to machine. In addition, apprentices learn how to use Computer Assisted Design and Computer Assisted Manufacturing on the modern milling and turning machines the university has invested in this year.
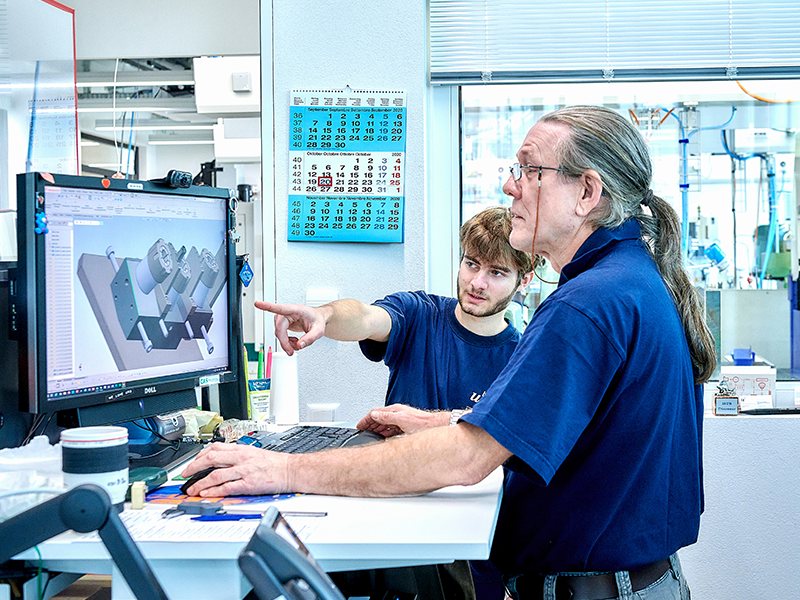
Meanwhile, rock music throbs from the radio in the workshop. The spirits are high, and the apprentices move confidently between the heavy equipment to extract tiny metal objects that will one day become tooth crown holders, heart valve hinges or fixtures on guide rails for minimally invasive surgery.
"Without the apprentice training and without their performance - for example, on the parts of the Rosetta space probe - the University of Bern would not be where we are today."
– Urs Rohrer
"I don’t have to be on top of everything,"chuckles Urs Rohrer as he sees how an older apprentice answers the question of a younger one. "But one thing needs saying: We have outstanding apprentices whose work has won several awards! Without the apprentice training and without their performance - for example, on the parts of the Rosetta space probe - the University of Bern would not be where we are today.”
From the idea to the product
The ARTORG workshop "Mechanical Design & Production" designs and manufactures complex mechanical components and devices for biomedical research and clinical application. The workshop at sitem-insel has been accredited as an interdisciplinary research platform of the SISF and is open to all researchers from the University of Bern, the Inselspital, Bern University Hospital, and sitem-insel who wish to implement medical technology projects and who require advice in conception and development as well as know-how in prototyping and production. The workshop is equipped with state-of-the-art Computer Numerical Control (CNC) lathes and milling machines. It supports research projects for medical technology development from conception to production, assembly and optimization in close collaboration with the user. It trains polymechanics EFZ apprentices with a focus on single part and prototype construction, who are trained in computer-aided design and manufacturing.